GZL series dry rolling granulator
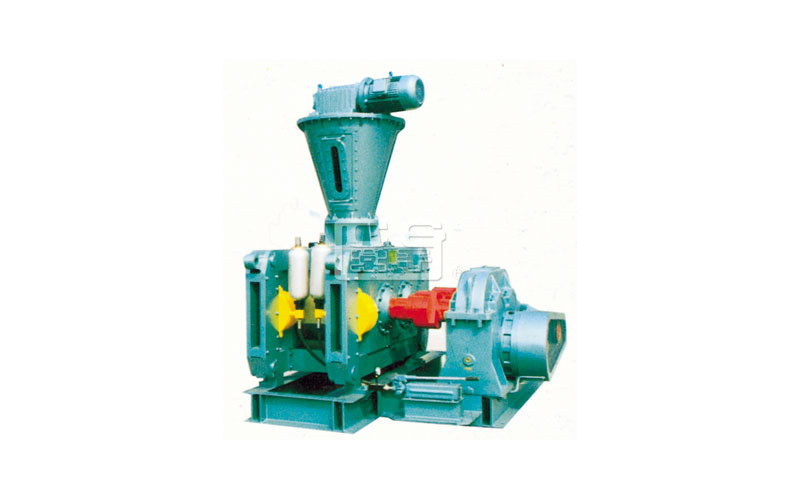
S
UMMARIZE
SUMMARY
Reliable supplier of drying equipment users
UMMARIZE SUMMARY
GZL series dry rolling granulator adopts the dry extrusion technology to compress the powder with water content less than 10% into pieces, and then through the crushing, pelletizing and screening process, to make the piece and block materials into the granular materials that meet the use requirements.
Dry rolling granulation is mainly by external pressure, so that the material is forced to pass through the gap between two reverse rotating rollers and compressed into pieces. In the rolling process, the actual density of the material can be increased by 1.5-3 times, so as to achieve certain strength requirements.
P
RINCIPLE
PRINCIPLE
Reliable supplier of drying equipment users
RINCIPLE PRINCIPLE
All kinds of dry powder materials are added from the top of the equipment, and enter two equal rolls through degassing and screw preloading. The rolls rotate relatively, and the material section is forced to enter between the two rolls. The rolls bite the materials into the roll gap for compression. After the materials pass through the compression area, the surface tension and gravity of the materials make them naturally come out. After being separated, the finger like lumps enter the crusher and are broken by the rotating knife row, and the broken materials enter the pelletizer and pass the rolling knife row to make the particles and some powdery materials enter the rotary vibrating screen for screening. Qualified products are sent to the finished product warehouse by conveyor. Powder: the material under the barking screen is sent back to the raw material bin for secondary rolling through the conveyor. The size of the extrusion pressure can be adjusted by the pressure of the hydraulic cylinder according to the needs of the granulation operation.
The sheet, strip and flat spherical materials can be obtained by changing the slotting form of the roll surface.
P
ARAMETER
PARAMETER
Reliable supplier of drying equipment users
ARAMETER PARAMETER
Item / parameter / model | GZL-240 | GZL-360 | GZL-450 |
Roll diameter mm | Φ240 | Φ360 | Φ450 |
Effective roll bandwidth mm | 80-160 | 180-500 | 220-1000 |
Roll speed rpm | 15,20,26,32 | 14,18,24,30 | 10-25 |
^Forming pressure Mpa | 120 | 160 | 210 |
Maximum thickness of rolling platemm | 4 | 8 | 8 |
Rolled sheet yield kg/h | 200-500 | 500-3000 | 800-5000 |
Product granularity mm | 0.5-6 | 0.5-8 | 0.5-6 |
Output of finished products kg/h | 160-400 | 400-2400 | 680-4000 |
Host power kw | 7.5 | 22-37 | 45 |
Total installed capacity kw | 20 | 50 | 80 |
size (LxWxH) mm | 1500×1300×5000 | 2000×2000×9000 | 2500×2500×10000 |
重量 t | 6 | 10 | 13 |
A
PPLICATION
APPLICATION
Reliable supplier of drying equipment users
PPLICATION APPLICATION
Petrochemical, fine chemical, medicine, food, metal powder
Bioengineering, pesticides, fertilizers, minerals, coal
![]() | ![]() |
F
EATURE
FEATURE
Reliable supplier of drying equipment users
EATURE FEATURE
The material can be compressed by mechanical pressure, without any wetting agent, and the purity of the product can be guaranteed.
Dry powder can be made directly without subsequent drying process, which is more conducive to the connection and transformation of the existing production process.
The particle strength is high, and the increase of bulk density is more significant than other granulation methods. Especially suitable for the occasion of increasing the proportion of product accumulation.
It can control environmental pollution, reduce powder waste and packaging cost, and improve product transportation capacity.
Compact structure, convenient maintenance, simple operation, short process, low energy consumption, high efficiency, low failure rate, suitable for a wide range of raw materials, roller pressure can be freely adjusted according to different materials.
The feeding and feeding device adopts frequency conversion stepless adjustment control, with high degree of automation, which can realize the control of one person and multiple machines, low labor intensity and long-term continuous operation.
The main transmission parts are made of high-quality alloy materials, stainless steel materials, titanium materials, chromium and other surface alloys, greatly improving the wear resistance, corrosion resistance, high temperature resistance and pressure resistance, so that the machine has a long service life.
P
rocess
PROCESS
Reliable supplier of drying equipment users
rocess PROCESS
The material can be compressed by mechanical pressure, without any wetting agent, and the purity of the product can be guaranteed.
Dry powder can be made directly without subsequent drying process, which is more conducive to the connection and transformation of the existing production process.
The particle strength is high, and the increase of bulk density is more significant than other granulation methods. Especially suitable for the occasion of increasing the proportion of product accumulation.
It can control environmental pollution, reduce powder waste and packaging cost, and improve product transportation capacity.
Compact structure, convenient maintenance, simple operation, short process, low energy consumption, high efficiency, low failure rate, suitable for a wide range of raw materials, roller pressure can be freely adjusted according to different materials.
The feeding and feeding device adopts frequency conversion stepless adjustment control, with high degree of automation, which can realize the control of one person and multiple machines, low labor intensity and long-term continuous operation.
The main transmission parts are made of high-quality alloy materials, stainless steel materials, titanium materials, chromium and other surface alloys, greatly improving the wear resistance, corrosion resistance, high temperature resistance and pressure resistance, so that the machine has a long service life.